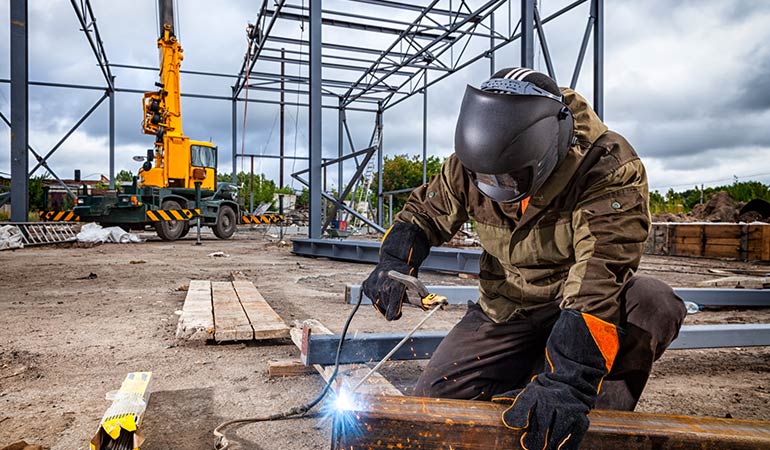
Alevac Series Dry Screw Vacuum Pumps
Designing, analyzing, producing, and maintaining mechanical systems require the use of engineering, physics, engineering mathematics, and materials science concepts. Mechvactech is a world leader in producing world-class quality vacuum pumps and systems and offering top-notch services.
Dry vacuum pumps have an oil- and liquid-free sealing system and are non-contact vacuum pumps. They achieve a clean vacuum without any oil or water back-flow or diffusion. These pumps are simple to use since they don’t need routine maintenance like refilling or replenishing water or oil.
Since it enables quick, clean depletion of gas from analyzers like mass spectrometers and electronic microscopes, their applications have increased recently. They are employed in a range of different applications, such as vacuum drying operations and film coating processes since they can produce clean vacuums and make maintenance simple.
Mechvac tech’s dry vacuum pumps provide advantages including low energy usage and a small design that are employed in many industries.
This device increases compression efficiency and delivers low power consumption because of its distinctive optimized rotor design. The dry vacuum pumps’ small, lightweight form makes them simple to install, even in tight locations. They may easily be moved.
A dry vacuum pump is a kind of vacuum pump that evaporates water from a substance using heat energy. Doing this produces a vacuum is produced inside the machine, which permits air to move through the system.
A dry vacuum pump is a tiny vacuum pump that has a moisture separator installed inside of it to capture moisture and other soluble slurry particles.
In order to save downtime, dry vacuum pumps are crucial for offering a high degree of pumping capacity. One can get several advantages by employing a dry vacuum pump. These pumps improve several agricultural applications while favourably impacting projects. Dry vacuum pumping installations are often located inside buildings to protect the pumps from the elements.
Two interlocking, screw-shaped rotors that revolve in opposition to one another make up a dry screw vacuum pump. The process vapours are sucked in, condensed, and then transferred to the gas outlet after being stuck between the cylinder and screw chambers. During the compression operation, neither the screw rotors nor the cylinder comes into touch. This is made possible by precise production and little room between the moving parts.
Benefits of Dry Vacuum Pumps:
- Dry compression, no contamination or reaction possible between process gas and operating fluid
- The Ultimate vacuum
- Energy efficient
- Can be designed for nearly all process gases thanks to material selection and temperature regulation
- They can be rotary air-seal tightly coupled pumps, positive displacement pumps, or submersible pumps.
Dry pumps maintain the product’s chemistry pure by reducing process contamination from oil and other chemicals. Booster pumps can be added to dry pumps to increase their capacity and expand their vacuum ranges. The lack of oil in these systems is a clear benefit.
Any lubrication is typically retained elsewhere, where it is less prone to contamination. Compared to oil-sealed pumps of comparable capacity, these pumps’ capacities are less and oil changes are less often.
Oil changes are typically the only maintenance performed, however, overhauls for bearing replacements need specialized equipment and knowledge.
Types of Dry vacuum pumps:
- Dry Screw Vacuum Pump
- Dry Claw Vacuum Pump
- Dry Scroll Vacuum Pump
- Roots Vacuum Pump
A Dry Screw Vacuum Pump consists of a cylinder with two rotating screw rotors. The gas is carried to the gas discharge after becoming caught between the cylinder and the screw chambers.
The screws must be maintained close together in order to generate a vacuum, usually with paper-thin clearances. Due to the tight tolerances, the product vapour has the propensity to polymerize or harden inside the pump, which can cause choking or jamming.
Dry vacuum pumps can readily withstand corrosive vapours with basic iron construction since they operate hot and corrosion often happens when there is moisture present. Manufacturing cast or ductile iron costs nothing and restricts thermal expansion. Due to the extreme thermal growth properties of stainless steel and other high alloy alloys, dry pumps cannot be produced from these materials.
Due to their design and metallurgy, dry vacuum pumps have consequently emerged as the preferred option for pumping some of the most aggressive process gasses or vapours in the chemical and process industries. These vapours are among the best suited for handling processes like distillation, solvent recovery, and crystallization.
Many sectors, including food processing, pharmaceuticals, and chemical manufacturing, employ dry vacuum pumping systems. These processes employ heat to remove moisture from the material, which leaves the machine vacuum-sealed. As a result, the material may be treated without risk of water pollution. The productivity of your product will be impacted by the dry vacuum pump you choose, so always opt for the greatest quality available.
Frequently asked questions
Dry screw pumps are positive displacement pumps that use a rotating helical screw to move fluid. They are often used in industrial settings for pumping thick or viscous fluids, and can handle high levels of solids without clogging.
The main advantages of dry screw pumps are their ability to handle high levels of solids without clogging, their relatively low cost, and their simple construction. They also have a good reputation for reliability and long life. However, they do require regular maintenance, especially if they are to be operated in dirty or dusty environments.
Dry screw pumps are positive displacement pumps that work by the introduction of a rotating screw into the fluid, which causes the fluid to be drawn into the pump and expelled through an outlet. The screw is rotated by an electric motor or engine, which gives the pump its name.
The screws on dry screw pumps are designed with helices that have a high degree of thread form, allowing for more efficient movement of fluid and higher volumetric throughputs. Additionally, dry screw pumps are capable of operating in high-viscosity fluids and can handle solid particles without damage. They are commonly used in oil and gas production, water treatment, and other industrial applications.
Dry screw pumps have a number of benefits over other types of pumps, including:
- They are less likely to cause corrosion or damage to the material being pumped.
- They can handle solids as well as liquids, making them perfect for pumping viscous or dirty fluids.
- Their moving parts are completely enclosed and protected, which makes them ideal for use in harsh environments.
- They are capable of high flow rates and can achieve very high pressures.
- They are relatively simple machines and require minimal maintenance.
- They are highly efficient, resulting in lower energy costs.
- Their construction makes them very durable and long lasting.
- They can be used in a wide variety of applications, from food processing to industrial production.
Dry screw pumps are a type of rotary positive displacement pump that use a rotating screw to move fluid through the pump. They have a wide variety of applications in both industrial and commercial settings. One of the main benefits of dry screw pumps is their ability to handle high viscosity fluids. However, there are a few potential drawbacks to using them.
One downside is that they can be expensive to purchase and maintain. Additionally, they can be noisy and require specialised motor starters. They also generate heat while operating, which can increase the temperature of the fluid being pumped.
Dry screw pumps are used extensively throughout the chemical, petrochemical, and refining industries. They are also popular in the power generation and water treatment sectors. Some of the other industries where dry screw pumps are commonly used include pulp and paper production, food processing, and metalworking.
Dry screw pumps are a good choice for certain applications because they offer high efficiency and can handle both liquid and solid material.
Dry screw pumps are made up of two screws that rotate in opposite directions. This design helps to create a vacuum, which in turn draws the material into the pump. The screws also help to break up the material, which makes it easier for the pump to handle.
Dry screw pumps are very efficient, meaning that they can move a lot of material with very little power. They can also handle both liquid and solid material, making them a good choice for many different applications.