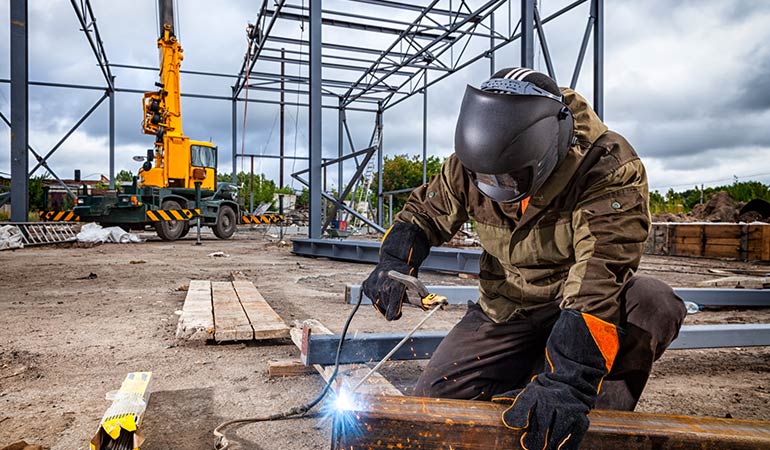
Dry Claw Vacuum Pumps
Every industrial vacuum furnace system employs a main (aka mechanical) pump, sometimes known as a “backing” pump when used in series with a booster pump or in combination with a booster and high vacuum pump combination, such as a diffusion pump.
These primary pumps are further classified as “wet” (oil-sealed rotary vane design or liquid ring pumps) or “dry”. The claw pump and the screw pump are the most common types of dry main pumps.
Dry pumps are becoming more common as an alternative to oil-sealed rotary vane pumps in several medium and high vacuum applications. Dry claw vacuum systems have grown to be a significant participant in the market in recent years.
With the least amount of maintenance needed, this technology gives the best level of energy efficiency. This is because of the pump’s novel non-contacting, dry compression, and positive displacement design.
Claw pumps are thought of being dry, positive displacement vacuum pump technology. Wet pumps (such as liquid ring pumps) employ oil, water, or other fluids as a lubricant and to assist create a seal; dry pumps do not expose the gas being moved to these lubricants.
Positive displacement in this context refers to the pump’s ability to physically capture a volume of gas and move it through it, resulting in low pressure at the input side of the pump.
Because of this, they are incredibly strong and able to survive challenging working circumstances. Dry claw pumps provide compression and expansion using two counter-rotating components, just like the rotary tooth compressor.
With little space between the claws, the rotors are pressed together but are not in contact. The claws include an entrance that allows air to enter when they spin inside the housing. The pump concurrently compresses another air pocket with each fresh intake.
With each complete revolution of the claws, there are two compression cycles. Dry claw pumps are perfect for applications requiring little maintenance and greater process compatibility.
They are more effective than certain other types of pumps, such as the rotary vane pump, and are suitable for tough conditions like wastewater treatment facilities.
Contamination of the pushed gas is prevented in all dry pumps. This has the benefit of lowering the condensation of pumped vapours and associated pollution.
The pump’s capacity to take high-temperature gases that might otherwise condense at lower working temperatures is also improved by the increased operating temperature. For the same reason, the claw pump offers advantageous properties for pumping water vapour as well.
Scrapers are another component of claw pumps that helps avoid the development of particulates. On the exterior of the rotors, where they are closest to the housing, there are a few tiny raised protrusions. The scraper mechanically removes any particles from the housing since the space between the scraper and housing is even lower than the clearance between the rotor and housing.
Claw pumps have the potential for auto-ignition when flammable gases are present because of their high working temperatures. Additionally, due to their high operating temperatures, close-running components may accumulate polymerization of process gases, requiring extra maintenance. Cool-running claw pumps are ideal in these circumstances.
The sophisticated claw rotors never make direct touch with the cylinder they are rotating in or with one another. The pumping chamber experiences no wear at all. Vacuum performance is constantly excellent throughout the life of these pumps since the chamber doesn’t wear out. They don’t require operating fluids in the pumping chamber since they run dry and are air-cooled.
Benefits of Claw Vacuums:
- Minimal size and superior building
- Wear and replacement parts are significantly reduced by non-contact design.
- Dry-running refers to the pumping chamber having no lubricating or sealing oil.
- When using air cooling, there is no need for water.
- Continuously fast pumping rates
- Superior volumetric effectiveness
- Performs better in a hotter environment
- Long service life and little maintenance
- No bearing maintenance.
- Decreased energy expenses result from lower power demand.
- Intelligent silencer design allows for silent operation.
- A wide range of sizes is available for a number of various purposes
Your vacuum and overpressure equipment’s performance, effectiveness, and availability are all optimized and available at Mechvac tech. The dry claw pump system from Mechvac tech is built as a multi-claw system, making it simple to meet the unique requirements of a facility. By choosing them, you may save even more energy and money on energy.
Frequently asked questions
A dry claw vacuum pump is a type of mechanical pump that uses a gas to create a vacuum. It has two main components: the pump and the motor. The pump extracts air from the surrounding environment, while the motor provides power to turn the rotor that creates the vacuum.
Dry claw vacuum pumps are used in a variety of applications, including medical devices, laboratory equipment, and food processing. They are also commonly used in industrial settings to evacuate systems or tanks and to create a vacuum for welding and metalworking.
When looking for a dry claw vacuum pump, the most important factor to consider is the capacity of the pump. You want to make sure that the pump can handle the maximum volume of air that you need to evacuate.
Other factors to consider include:
- The type of connectors the pump has
- The type of vacuum gauge it uses
- The length of the power cord
- The weight and size of the pump
- The noise level of the pump
- The voltage and frequency requirements
It is also important to make sure that the pump you choose meets all safety regulations. It should have an overload protection switch, as well as adequate insulation, shielding and grounding protection.
A dry claw vacuum pump is a device that uses negative pressure to evacuate air or other gases from a sealed system.
They are commonly used in industrial and laboratory settings to evacuate systems such as piping, valves, and tanks. They can also be used to evacuate the air from a container of gas in order to create a vacuum. This can be useful for creating a vacuum environment for testing or manufacturing purposes.
It is easy to maintain a dry claw vacuum pump. All you have to do is keep the pump clean and free of dirt and debris. Make sure to check the oil level regularly and change the oil when needed. Also, be sure to keep the air filters clean.
If you take care of your vacuum pump, it will last for many years. Dry claw vacuum pumps are built to last and are very reliable machines. So if you take care of it, it will take care of you.
There are some potential downsides to using a dry claw vacuum pump. One is that they can be quite noisy, so they may not be suitable for use in certain settings. Additionally, they can be difficult to operate and require a certain level of expertise to use them correctly.
Dry Claw Vacuum Pumps are a specific type of rotary vacuum pump. They are used to evacuate systems by creating a partial vacuum. This can be accomplished in one of two ways:
- The first way is to seal the pumping mechanism inside the evacuated system. When the pump is turned on, it creates a vacuum on the atmospheric side of the seals which draws fluid out of the system.
- The second way is to use an exhaust port located outside of the evacuated system to draw air in and create a vacuum on the atmospheric side of the exhaust port. This method is often used when it is not possible or desirable to place the pump inside the evacuated system.
Dry Claw Vacuum Pumps are considered to be one of the most reliable and efficient types of vacuum pumps. They are also relatively quiet, making them ideal for use in residential or office settings. Finally, they can be used with either a single phase or three phase power supply, allowing maximum flexibility when choosing the right pump for any application. Overall, dry claw vacuum pumps are a great choice for anyone needing to evacuate air or other gases from a sealed system.